Monik Sheth, Co-Founder & CEO of Ultralight Labs
Jul 15, 2024
Design controls can rank fairly high on the list of things that medtech engineers dread, alongside recurring meetings and sales teams that overpromise product delivery timelines.
But in our many conversations with engineering teams, we’ve learned that most of this dread comes down to a lack of understanding and tooling.
Design controls might seem like bureaucratic overhead, but in reality, they're the backbone of successful medical device development. If you're an engineer, understanding design controls is essential. Let's cut through the noise and get to the essence of what you need to know.
Design Control Basics
Design controls are structured practices and procedures that ensure your medical device is safe, effective, and compliant with regulations. Think of them as your product roadmap embedded with some predefined rules, guiding you from concept to market.
The diagram below, which is perhaps difficult to follow, is actually a gross oversimplification of how device companies need to manage their data & documentation flows for design controls and how that flows into a broader quality management process.
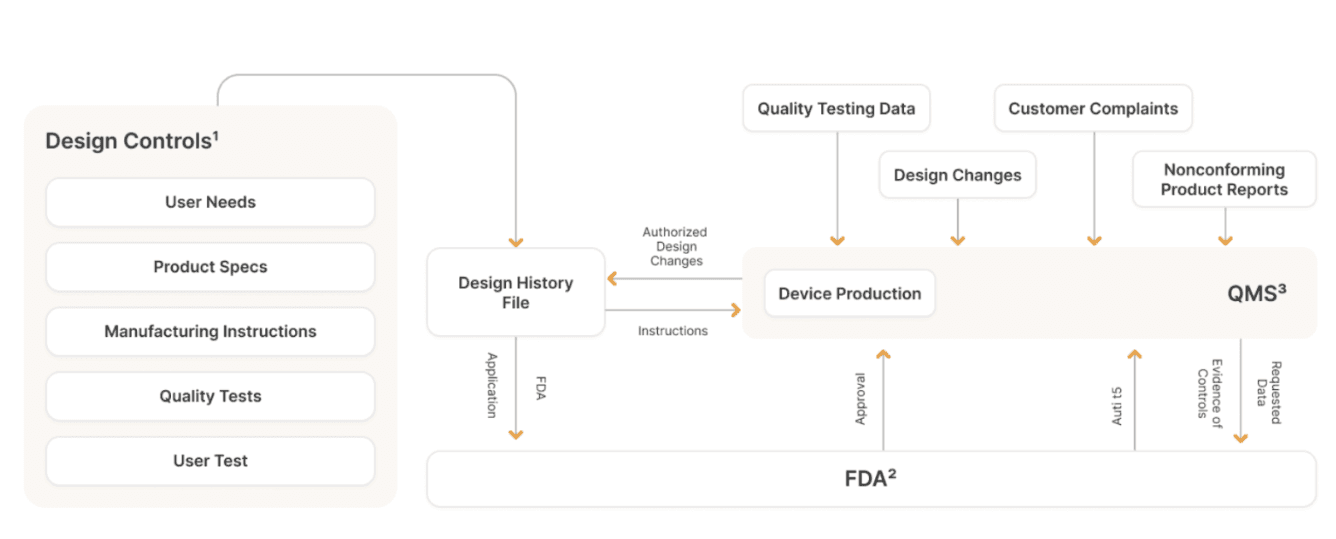
Key Elements
Design and Development Planning: Start with a plan. Outline your design and development activities. Assign responsibilities. This isn’t just paperwork; it’s about having a clear path and updating it as you go.
Design Inputs (e.g. User Needs, System Requirements, Subsystem Requirements): Inputs are your device's requirements. They come from user needs, intended use, and regulations. Get this right, and you have a solid foundation. Get it wrong, and you’ll face endless revisions.
Design Outputs: Outputs are your blueprints—drawings, specifications, instructions. These must match your inputs. Think of it as aligning your vision with reality.
Design Review: Regular reviews are essential. Gather your team and review your progress. This keeps you on track and catches issues early.
Design Verification: Verification checks that your outputs meet your inputs. It’s the step where you ensure what you’ve designed matches what you planned to design. Each requirement must be verified.
Design Validation: This is about the real world. Does your device meet user needs? This is tested under actual or simulated conditions. Each user need must be validated.
Design Transfer: This is the handoff from design to production. Your design needs to be accurately translated into manufacturing specifications.
Design Changes: Changes are inevitable. Manage them with clear procedures. Document, validate, and approve every change to keep everything under control.
Design History File (DHF): The DHF is a comprehensive record of the design process. It’s proof you followed your plan and met regulatory requirements.
On Requirements Traceability
Requirements traceability refers to the process of documenting and linking every requirement for a medical device through every stage of its development and lifecycle. This includes capturing and connecting requirements from the initial design, through development, testing, and eventual deployment and maintenance.
Think of it as a map or a family tree for the device’s requirements. Each requirement is linked back to its source (like user needs or regulatory standards) and forward to its corresponding outputs (like test results or product specifications). This makes it easier to see how each piece of the device was designed to meet specific needs and standards, and it helps ensure that nothing is overlooked throughout the device’s development and approval process. This traceability is crucial for maintaining high quality and compliance with regulatory standards in the medical device industry.
But given even a simple device can have hundreds to thousands of requirements–and thus many thousands of dependencies–managing traceability in Excel, Word, or a suboptimal tool can be a painful and error-prone exercise.
Finding a way to thoughtfully establish traceability, maintain version history, and easily generate specification files and regulatory documentation can have a tremendous impact on the speed and quality of product development.
This comprehensive approach not only accelerates release cycles but also enhances compliance and traceability, allowing teams to focus on innovation and quality.
Tips for Implementation
Start Early: Integrate design controls from day one to avoid last-minute chaos.
Documentation is Key: Detailed records are invaluable—not just for compliance, but for understanding your own process.
Cross-functional Teams: Bring in diverse perspectives. This avoids blind spots and improves your design.
Regular Reviews: Frequent reviews catch problems early and keep you on course.
Continuous Improvement: Use feedback to improve. Always look for ways to refine your processes.
How Software Tools Help
Design controls aren’t about jumping through hoops. They’re about ensuring your device works and is safe. For engineers, this means fewer surprises and a smoother path to market.
But imagine organizing all of this data and documentation manually without good tooling. Most medical device teams navigate design control via manual, paper-based processes or clunky point solution software systems that aren’t optimized for modern engineering requirements management. In either case, lots of human resources are wasted. And product data & workflows are siloed across different teams & systems.
Software tools for design control can streamline this process by providing a centralized platform for documentation, collaboration, and compliance management. These tools automate many of the tedious aspects of design control, such as tracking changes, maintaining version control, and ensuring that all necessary reviews and approvals are completed. They also facilitate real-time collaboration across cross-functional teams, making it easier to gather input, conduct reviews, and implement changes efficiently. And a few select tools–Ultralight included–even simplify the process of managing traceability via an intelligent user interface that helps organize, visualize, and suggest traces.
By using these tools, engineers can focus more on innovation and less on administrative tasks, ultimately speeding up the development process and reducing the risk of errors.


Select Screenshots from Ultralight's Design Control Hub
Design controls are essential for medical device engineers. By integrating these practices into your workflow and leveraging software tools, you’ll navigate the complexities of device development with confidence.
Want to dive deeper? Reach out and we’ll walk you through how we’ve helped dozens of teams implement more streamlined processes for design control. Book a demo here.